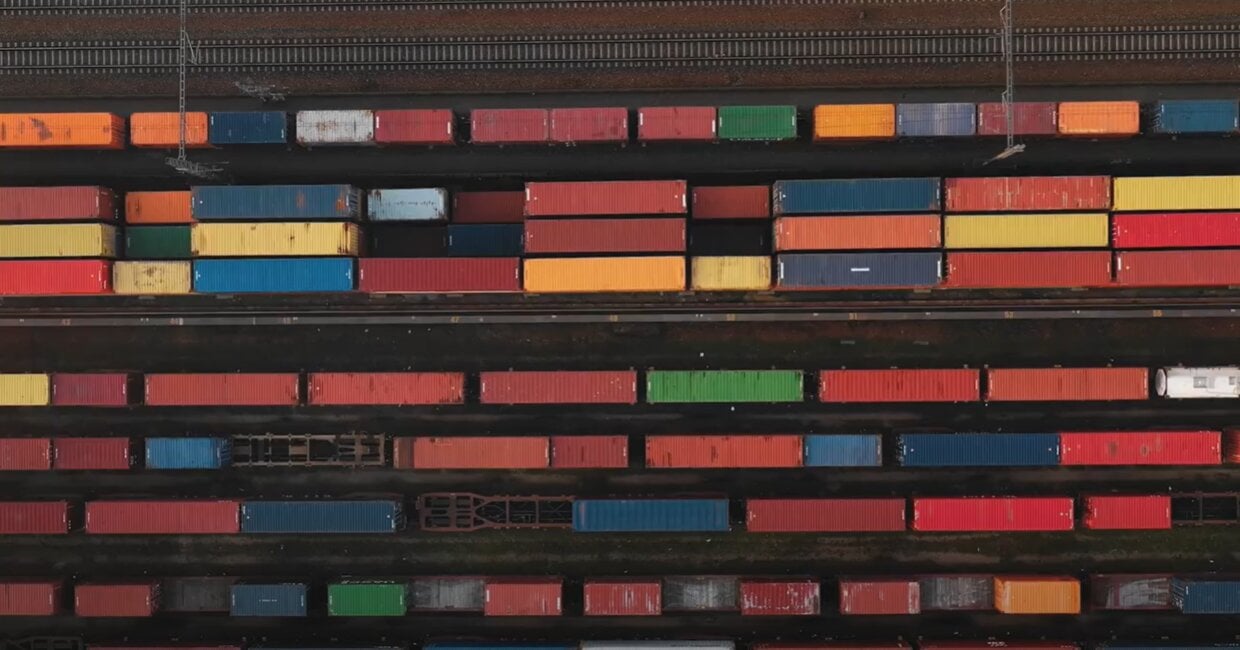
Keeping rail cargo on track with Kalmar SmartPort process automation
With the introduction of a number of new features specifically designed for rail operations, there’s never been a better time for railroad companies and container terminals that count rail as part of their transport mix to take advantage of process automation. In this article we look at how our SmartPort offering can improve visibility and efficiency for operations teams and equipment operators alike.
Whether we’re talking about a rail yard or a marine or intermodal terminal, process automation provides operators with the visibility they need to improve equipment utilisation, reduce turnaround times and congestion, and provide better service to their customers. It does so by automating manual processes that can act as bottlenecks and enabling data to be gathered that will help customers optimise their flows.
Kalmar’s SmartPort suite of process automation solutions is already helping terminal operators of all sizes and types to drive their businesses forward by enabling safer, more secure and more efficient operations. And now we have introduced new features specifically developed to bring the same benefits to rail operations.
“We have worked together with selected major railroad operators in the US and Canada to adapt our products specifically to address the needs of rail operations"
“As railroads begin to transition from wheeled to stack operations we have seen them encounter challenges with their terminal operating systems (TOS), which have struggled to keep track of stack inventories in a rail environment,” says John Scott, Vice President, Automation Sales, Americas, Kalmar. “We have worked together with selected major railroad operators in the US and Canada to adapt our SmartMap and SmartScreen products specifically to address the needs of rail operations. Essentially, what we can now do is model a train in the rail yard in the same way that we can already model a container stack in a marine terminal to provide complete visibility over operations – from a high-level view of the yard right down to the level of an individual railcar, rail well or container.”
Better visibility over rail yard operations
Kalmar SmartMap is a real-time visualisation and operational tool that provides terminal operators with the current location and status of all equipment in the yard that is fitted with location hardware. With a Kalmar SmartTrack licence operations teams can view the location of railcars in the yard and the inventory of the containers loaded on them.
The system displays the railcars, rail wells and containers on the tracks. Users can also drill down to see details of the rail wells and the containers on them as well as information on whether or not a car or rail well is damaged and should be treated with caution.
SmartMap displays the current and historical equipment location and includes essential map functionalities like zooming and panning. Operations staff can also view current or historical traffic patterns to help with identifying congestion issues or traffic problems.
Bringing visualisation to the equipment cab
For equipment operators, Kalmar’s latest offering brings an unprecedented level of visibility into the cab through the Kalmar SmartScreen application. The operator can view a list of jobs from the TOS and automatically filter them based on location, proximity or priority. When a job is promoted it automatically goes to the top of the list and is highlighted in red. The operator can also see which containers to deliver and which containers not to bury based on pending moves.
“SmartScreen helps equipment operators to prioritise their work. For example, an operator can filter their job list by train departure time and destination and immediately see the location of all the containers they need to attend to for that departure. This saves a tremendous amount of time by eliminating the need to search through a long list of jobs to find the right one,” says Angelica Nieto, SmartPort Product Manager at Kalmar.
The rail view in SmartScreen displays all the relevant railcar information including the ID, well number, sequence and the containers it is carrying. A scrollable visual model of the train can also be used to locate a specific car. To confirm a container as lifted or set, the operator simply uses the on-screen prompts.
“SmartScreen for rail operations puts all the information that equipment operators need to do their job safely and efficiently at their fingertips,” Angelica explains. “For example, with information like the container weight and railcar capacity visible the operator can avoid the risk of overloading a car. SmartScreen also increases safety by alerting operators to any damaged cars or wells.”
The smarter way to manage your rail yard
To take advantage of these new features, rail operators need to have SmartStack implemented for their wheeled lifting equipment and a SmartTrack licence. Implementing SmartStack involves installing GPS on lifting equipment to monitor its location and sensors to monitor components such as the twist locks and spreader – as well as an in-cab screen if one isn’t already installed. Kalmar can train the customer’s mechanics to install the necessary hardware or provide mechanics to perform the work on the customer’s behalf.
For customers that are already using SmartStack and SmartMap, all that’s required is a SmartTrack licence.
“There are many examples of marine and intermodal terminals around the world that have boosted productivity in their container yards with the help of SmartPort products, and now we can extend the same level of functionality to rail operations too,” says John. “Our ultimate aim is to give customers who have rail in their transportation mix the tools they need to make the next leap in terms of smart decision-making, operational efficiency and safety.”
Learn more about SmartPort process automation solutions here.
Related articles
Further reading
Subscribe and receive updates in your email
Meld je aan voor onze publicaties